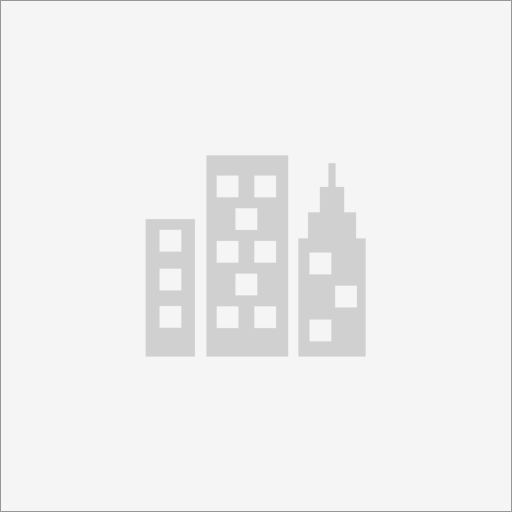
Multisorb Technologies
jobs-near-me.org
Overview
The Electrical Controls Engineer is responsible for designing, developing, programming and troubleshooting control systems throughout the manufacturing facility. The Engineer be responsible for developing machine designs starting from the design input phase through validation/production handoff activities. The Engineer will also be responsible for continuous improvement initiatives by implementing machine upgrades to both custom built machines as well as off the shelf/purchased machines to improve productivity as well as safety. The position also requires regularly assisting the Maintenance staff with electrical troubleshooting of the various machines in the facility.
Responsibilities
- Assists the Project Engineering team with developing design inputs from operations, developing electrical and pneumatic BOM’s and schematics, mechanical assembly, wiring, programing PLC and HMI control systems, debug/troubleshooting, assisting Manufacturing Engineers with writing QWI’s and preventative maintenance procedures and assisting Quality with validation activities.
- Coordinates equipment upgrades on custom built or off the shelf machines requiring new electronics and/or updates to PLC, HMI, vision or servo drive programs.
- Develops and implements custom testing fixtures/equipment for Maintenance and Quality.
- Recommends changes to equipment which will increase quality, productivity, efficiency and safety.
- Assist the Maintenance team with daily electrical troubleshooting and equipment breakdown issues.
- Maintains engineering documentation including drawings, schematics and BOM’s.
- Assists in operator training on new machines and updates to current machines.
- Supports Tool Crib Attendant on spare parts inventory requirements as well as identifying replacements for obsolete machine components.
- Supports Quality Engineering on complaint investigations and corrective actions.
- Understand and comply with all applicable requirements of the Company’s ISO/cGMP quality system as documented in the Quality Manual, System Procedures, and Work Instructions
Qualifications
- Knowledge of processes utilizing custom automatic equipment including hydraulic, pneumatic, and electronic control circuits.
- Experience with Allen Bradley control systems including PLC’s, HMI’s, servo drives. This includes experience with RSLogix500, RSLogix5000, Studio5000, PanelBuilder and Devicenet.
- Experience with Cognex and Keyence vision systems.
- Experience with Indusoft HMI development software.
- Experience with servo, stepper, AC and DC motors and drives.
- Ability to create or update electrical schematics.
- Proficient in 2D AutoCAD and/or Autodesk Inventor.
- High mechanical aptitude with hands-on experience.
- Good verbal and written communication skills
- Proficient with Microsoft Office applications.
- Experience directly supporting manufacturing processes and equipment.
- Knowledge of physics, mathematics, chemistry, electronics, pneumatics, and hydraulics.
- Experience working with ERP systems, InfoXA is a plus
More About Filtration Group
Filtration Group is on a mission to make the world safer, healthier and more productive. With a passionate workforce, global footprint and world class engineering and manufacturing capabilities, we are driving innovation and developing solutions across a broad spectrum of applications in the fast-growing and rapidly-evolving global filtration industry. We are committed to maintaining an entrepreneurial culture built on a foundation of trust and in which our leaders exhibit a strong bias for action.
The Company began in 2009 and has rapidly grown organically and through a thoughtful acquisition strategy to be a global leader in the highly attractive filtration industry. Filtration Group has the broadest portfolio of solutions in the industry and has had a particular focus on building a leading platform of solutions focused on the Life Sciences and Indoor Air Quality end markets which are rapidly growing in the current market environment. Filtration Group produces mission critical products with high replacement rates. Over 80 percent of the Company’s revenue comes from replacement / consumable products, many of which are specified into customer’s products or processes. With revenues over $2 billion, Filtration Group is consistently recognized as the fastest growing and one of the largest filtration businesses in the world and has a global footprint of 141 facilities in 28 countries. Filtration Group has over 10,000 employees who are united in their Mission to make the world safer, healthier and more productive.
Apply
To help us track our recruitment effort, please indicate in your cover/motivation letter where (jobs-near-me.org) you saw this job posting.